B2B last-mile delivery: how to optimize logistics
Content Writer
Modern customers are not willing to wait, especially in the B2B segment. Imagine ordering crucial parts for production, but their delivery is delayed by hours or even days. This could paralyze the entire production process. That's why last-mile delivery has become a serious challenge for B2B companies. How can you ensure fast and reliable delivery without unnecessary costs? This question troubles many business owners, particularly in the e-commerce sector.
In B2B last-mile delivery, speed is important, but so are adaptability and efficiency in logistics solutions, which directly impact business reputation and customer satisfaction.
To stay competitive, B2B companies are forced to rethink their approaches to last-mile logistics. This is not just transportation; it’s a strategic task that requires modern technologies, flexible delivery models, and proactive inventory management. Companies that quickly adapt to changes and effectively integrate new solutions will gain a significant market advantage.
This article will help you dive into last-mile logistics optimization, revealing key challenges, new trends, and practical strategies that will not only keep your business up to date but also ahead of competitors.
What is meant by B2B last mile delivery?
B2B last-mile delivery is the final stage in the supply chain, where goods are delivered from a distribution center to the customer’s address. This is a critical phase because today’s customers expect fast delivery – within a day or even a few hours. This final leg of the journey carries the highest logistical burden.
In B2B, it’s about large volumes of specific goods that require special transportation conditions. These might include oversized loads, hazardous materials, or equipment needing special packaging. Tight deadlines, personalized customer requirements, and the need to maintain the integrity of goods significantly complicate this process. Delays or damage to goods can lead to disrupted production schedules, penalties, loss of reputation, and, ultimately, loss of clients.
For example, delivering industrial parts may require synchronization with the production line, which involves not just timely delivery but also ensuring the availability of loading platforms, adherence to transportation norms, and other requirements.
Primary challenges of B2B last-mile delivery
B2B last-mile delivery faces significant challenges that can impact the efficiency and success of business processes. Statistics show that this process accounts for nearly half of all logistics costs. It directly affects the reputation of a B2B company and customer satisfaction. Therefore, solving these issues to maintain high service quality and optimize costs is a serious task for suppliers.
Let’s explore the most common last-mile delivery challenges.
Poorly planned delivery routes
Unoptimized delivery routes are one of the most common factors negatively impacting the efficiency of logistics operations in the B2B segment. The lack of well-designed routes leads to several issues, including:
- Increased operational costs.
Inefficient use of vehicles drives up fuel expenses, vehicle wear and tear, and driver wages. Additionally, there is a higher risk of incurring extra costs related to downtime, traffic violation fines, and other unforeseen situations. - Delivery delays.
Failing to meet delivery schedules harms the company’s reputation and customer satisfaction. Delays can disrupt clients' production processes, potentially leading to financial losses and a loss of trust. - Decreased fleet productivity.
Inefficient use of vehicles reduces their productivity and shortens their operational lifespan. - Complexity in managing logistics processes.
A lack of clear route planning makes it difficult to monitor order fulfillment, predict costs, and respond quickly to changes in operating conditions.
Customer expectations: fast and cheap delivery
Modern B2B customers demand high-quality logistics services, expecting fast and economical delivery. However, combining high speed with low costs is a challenging task that requires careful planning and the use of modern technologies.
Challenges in meeting customer delivery expectations:
- Conflict between speed and cost.
Fast delivery typically comes with additional expenses for fuel, driver wages, and the use of faster modes of transport. Conversely, reducing costs can extend delivery times, creating a need to find a balance between these factors. - High service quality expectations.
Customers expect not only fast delivery but also the integrity of goods, adherence to storage conditions, and real-time tracking of the shipment's location. - Individual customer needs.
Each customer has their own delivery requirements, making it difficult to develop universal solutions and necessitating a flexible approach to each order.
Difficulties with cost control
Cost control in last-mile delivery can be problematic due to various factors. These include traffic congestion, delays in modern high-rise buildings, aligning with clients' production schedules, large shipment sizes, and complex inventory management in distribution centers. Companies often find it difficult to adapt their logistics to clients' demands for fast delivery. This leads to significant increases in last-mile logistics costs and, consequently, reduced competitive advantages.
Use of outdated delivery methods, lack of flexibility
Outdated delivery methods and a lack of flexibility can hinder achieving high efficiency. Without modern logistics solutions and technologies, improving delivery processes and ensuring adaptability to changing business and customer needs is impossible.
Addressing last-mile delivery challenges is crucial for maintaining business competitiveness. To stay ahead, companies must focus on optimizing delivery routes, meeting customer expectations for speed and cost, controlling expenses, and adopting modern delivery methods. Next, we will explore how to achieve high service quality and operational efficiency.
How to optimize B2B last mile delivery?
Optimizing the last-mile delivery process directly impacts the efficiency of B2B logistics operations. By implementing modern technologies and innovative approaches, businesses can significantly reduce costs associated with this delivery stage and improve customer service. Let's explore a few strategies to optimize the last-mile delivery process.
Route optimization
By utilizing advanced algorithms to determine the most efficient routes for delivering goods to customers, suppliers can calculate the cheapest and fastest delivery paths. These algorithms consider factors such as road conditions, vehicle capacity, traffic congestion, and delivery time windows. This approach reduces fuel costs, shortens delivery times, and increases vehicle operational efficiency.
For instance, DHL in Germany employs route optimization software, resulting in significant reductions in delivery time and fuel costs. Consequently, this logistics provider emphasizes the convenience, speed, and cost-effectiveness of its services.
Real-time tracking
Real-time tracking allows you to monitor the status of shipments as they happen. This ensures transparency and allows customers to see where their goods are at any given moment. Hermes uses parcel tracking apps that provide customers with real-time location data of their shipments.
Flexible delivery terms
By offering customers the flexibility to choose their preferred delivery time and location, or by utilizing delivery time windows, customer satisfaction is significantly increased. Suppliers can better adapt to specific customer needs over time. This simultaneously solves several challenges: reducing last-mile logistics costs, forecasting future deliveries, and creating the most favorable conditions for their business partners.
For example, logistics companies in Berlin offer deliveries within various time windows, allowing for better fleet planning, reduced delivery times, and prompt fulfillment of B2B customer needs.
Telematics integration
Telematics is like giving your cars a super smart brain. It uses tech to keep track of your vehicles in real time, from how fast they're going to how much gas they're burning. With this info, you can plan better routes, spot any car trouble right away, and keep your whole fleet running smoother.
Analytics
Data analytics helps in forecasting needs and managing resources. By collecting and analyzing data, companies can identify customer behavior trends, develop inventory management forecasts, and enhance their logistics strategies. In Germany, modern logistics companies use analytical platforms to gather current and historical data. This allows them to adjust delivery routes, forecast potential workload, reserve necessary truck fleets, determine required warehouse space, and more.
Auto-allocation of resources
Automatic resource allocation helps to use available resources efficiently. This process includes optimizing the use of vehicles and personnel. For instance, B2B companies can use software to automatically assign deliveries, reducing delays, cutting fuel costs, and improving vehicle load efficiency.
Delivery confirmation
Delivery confirmation ensures that goods reach their destination and are received. This often involves electronic signatures or photo evidence of delivery. In Germany, many companies have implemented electronic confirmation systems, allowing customers to track the timely receipt of their orders in real-time.
Reliable B2B logistics provider
Choosing a reliable provider is a critical factor for successful delivery. A reliable provider ensures a high level of service and can handle any challenges. In Germany, companies like DPD, UPS, and DHL are known for their reliability and high service standards.
Comparison of key delivery optimization strategies
Strategy | Description | Example (Germany) |
Route optimization | Planning efficient routes | DHL: routing algorithms |
Real-time tracking | Monitoring shipment in real-time | Hermes: tracking app |
Flexible delivery terms | Changing delivery times and slots | Delivery in various time slots |
Telematics integration | Collecting data on vehicle conditions and logistics | Telematics systems |
Analytics | Analyzing data for supply chain forecasting and management | Analytical platforms |
Auto-allocation of resources | Optimizing resource usage | Resource allocation software |
Delivery confirmation | Confirming receipt of goods | Electronic confirmation systems |
Reliable provider | Choosing a reliable logistics partner | DPD, UPS, DHL |
Conclusion
The business world today is spinning at an incredible speed, and customers are increasingly demanding instant delivery. That is why efficient B2B last-mile delivery has become a real challenge for companies.
To keep up with this pace, businesses need to constantly improve. The implementation of innovations such as driverless transport and intelligent route planning is already changing the rules of the game today. But this is just the beginning.
The future of delivery is a combination of technology and environmental friendliness.
Although technology opens up new opportunities for us, we should not forget about our planet. Alternative fuel vehicles and smart routing are not just trends but necessities.
Data is the new gold of logistics
By analyzing large amounts of data, B2B suppliers can optimize every step in the supply chain. This allows not only to reduce costs but also to anticipate customer needs, providing them with personalized service.
Best practices are the key to success
To be a market leader, it is not enough to simply implement new technologies. It is also important to adhere to the best management practices. This will not only increase efficiency but also create a strong team capable of implementing the most ambitious projects.
FAQ
What is the difference between the first mile and last mile?
The first mile refers to the initial stage of the shipping process, where products are moved from the manufacturer or supplier to the logistics hub. The last mile is the final stage, where goods are delivered from the hub to the customer's location. While the first mile focuses on bulk movement of goods, the last mile is concerned with efficient, timely delivery to the end consumer.
How long does last mile delivery take?
The time for last mile delivery can vary depending on several factors, including the distance to the customer, traffic conditions, and the delivery company's efficiency. Generally, last mile delivery can take anywhere from a few hours to a couple of days.
What is KPI in last mile delivery?
KPIs (Key Performance Indicators) in last mile delivery are metrics used to measure the efficiency and effectiveness of the delivery process. Common KPIs include delivery time, customer satisfaction, order accuracy, and cost per delivery. These indicators help companies optimize their delivery operations and improve overall service quality.
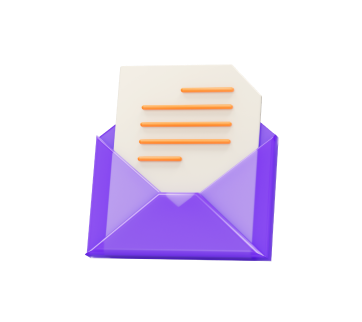