E-Commerce inventory management: peculiarities and strategies
Content Writer
- What is inventory management exactly?
- Definition of managing inventories in an online store
- How come inventory control is such a necessity if it's supposed to be so important?
- How do online retailers maintain track of their stock levels?
- The Three-Step Examine
- Evaluation of Stocks
- The term “economic order quantity”, or EOQ, refers to the least amount of a product that must be sold in order to turn a profit
- Similar terms: 3PL Manufacturing
- The FSN Procedure
- Compared: LIFO and FIFO
- JIT inventory management
- Forecasts of Interest
- Establishing an Infrastructure for Scanning
- Drop delivery
- Comparing quantity requirements and their economic equivalents
- Initial in, initial out
- Parallel docking
- Additional provisions
- MRP stands for Material Requirements Planning
- Inventory Management Software
- Utilizing optimal practices for inventory control
- FAQs
Technically speaking, E-commerce inventory (sometimes referred as stock) management refers to a method that uses a scientific approach to managing the stocking, storage, monitoring, and distribution of products for an online store. Industrial evidence suggests that E-commerce focused or related businesses that implement effective methods and tactics for inventory management may gain a competitive edge through increased output and decreased operational expenses. If businesses adopt these approaches, it may be possible to achieve this goal.
Retailers who do business online are required to have a website that is simple to use, a reliable transportation strategy, and accurate stock counts and locations. Sadly, the majority of these stores make expensive inventory errors in the beginning, such as failing to adopt an inventory management system. These errors can be avoided by following a few simple best practices or at least bearing those in mind.
The management of inventory includes each and every process that is carried out from the moment that items are acquired up until the point at which they are sold to the end customer. Alterations to the way inventory is managed have the potential to have a major effect on the bottom line, either positively or negatively. Inventory control has the potential to boost revenue when it is correctly executed. On the other hand, missing out on possibilities could end up being financially expensive.
E-commerce can help a company expand in many different ways, including the monitoring of stock levels in an online store, which is just one of the many ways it may assist in this process. Technology may help business owners improve their financial decisions and maximize the effectiveness of their warehouse operations. Technology can also assist business owners in maximizing their productivity.
What is inventory management exactly?
Inventory refers to the products you currently possess and intend to sell. Inventory management involves monitoring and storing products so that demand can be met promptly and effectively. Logistics is the study of the collection, storage, and processing of goods prior to their sale.
Practice suggest that up to several weeks may pass before improper inventory management becomes evident. Once they do appear, the outcomes can be undesirable: destroyed products, lost inventory, costly storage fees, or even worse, depleted inventory and unfulfilled customer orders. Yet, don't forget that holding costs and storage fees may reduce profitability.
Definition of managing inventories in an online store
It is crucial for the success of any business to maintain precise inventory counts. The front and back ends of your company are properly supported by the firm groundwork you've laid. This part of the supply chain connects your company's final clients with the companies from which it sources goods and services. For instance, it can keep you from losing consumers because of under or overselling on the front end of your firm.
Managing the nature, quantity, price, and location of a company's stock are the four cornerstones of effective inventory management in an online store. The online store's needs, such as inventory management across numerous marketplaces, are met by the e-commerce function. With the aid of the internet shop, these requirements can be fulfilled.
How come inventory control is such a necessity if it's supposed to be so important?
Any business would be foolish to undervalue its inventory. Manufacturing, food service, and retail can all feel the effects of inadequate stock levels. A company's inventory can act as both a boon and a bane. Deterioration, theft, and total destruction are all possible risks. Keeping a lot of stock on hand could hurt a company's capacity to generate a profit.
To effectively manage your ecommerce inventory, it is crucial to first gain a comprehensive understanding of your business's specific requirements and demands. It is important to initiate the search promptly once the designated time arrives. What is the purpose or significance? Inventory management is crucial for any company due to its extensive impact on various aspects of the business. Therefore, it should be considered a top priority for your organization.
Having a reliable inventory management system is crucial for all businesses, regardless of their size or industry. Implementing an inventory tracking system can enhance efficiency in managing inventory and enable more accurate price estimations. Furthermore, this feature provides the advantage of promptly responding to unforeseen changes in demand, without compromising product quality or risking customer dissatisfaction. Focusing more on their clientele is essential for companies that want to prioritize customer satisfaction.
How do online retailers maintain track of their stock levels?
When it comes to managing inventory for an online store, there is no one-size-fits-all solution. Different organizations require distinct inventory management strategies. Examine the options to determine if any of them align with the business's overall objectives.
The Three-Step Examine
The ABC Analysis procedure generates three classifications for stockpiles. The profitability of each SKU determines the category to which it belongs.
So, let's analyze this further. Category 1 assets may have both a high value and a limited supply. Category 2 inventory quantity and/or value may be intermediate. Category 3 may contain low-value, high-quantity inventory.
This method of stock organization facilitates the sale of multiple product lines across an organization. What does this even imply? because a variety of products means that replenishment strategies may be tailored to each form of stock.
In conjunction with an inventory management system, the ABC analysis technique enables more precise administration of the restocking of specific items.
Evaluation of Stocks
Inventory management software with less functions is preferred by new businesses and companies with fewer employees. On a consistent basis, the amount of stock on hand is measured against the predicted demand in the future. Manual labor is common, however stock reviews can assist define minimum stock levels that can be used to begin automatic inventory counts and replenishment as required. This can help cut down on the amount of time spent manually counting and replenishing supplies. Auditing the inventory takes a lot of time and is prone to making mistakes, but it can be helpful for keeping the order in the system that manages the inventory.
The term “economic order quantity”, or EOQ, refers to the least amount of a product that must be sold in order to turn a profit
When it comes to inventory management, this method is utilized to figure out how many of a particular item should be ordered in a single shipment of a greater quantity. In order to facilitate the completion of this computation, it has been presumed that the level of consumer demand will remain unchanged. The total cost of the model takes into account not only the money spent on the original purchase but also the money needed for initial setup and continuous storage.
The objective of the EOQ model is to guarantee that the correct quantity of inventory will be ordered for each shipment. This will ensure that neither too little nor too much inventory will be kept on hand. When initial investment and ongoing maintenance are limited to a bare minimum, it is believed that inventory costs will be reduced to a lower level.
Similar terms: 3PL Manufacturing
3PLs are companies that manage the logistics for online retailers on behalf of others.
For an agreed-upon fee, 3PLs will manage the warehouse, shipping, and other fundamental functions for online retailers.
The services offered by third-party logistics providers (or “3PLs”) range from basic to complex supply chain tasks.
The Third-Party Logistics industry will appeal to business owners who value big-picture pondering over minute details. For the return of their valuable time, they would willingly pay more.
If so, then you should read our detailed analysis of 3PL warehouse fulfillment logistics to determine if it is a good match for your eCommerce business.
The FSN Procedure
This type of inventory control involves keeping track of non-essential items that may be required in an emergency. The objects are then categorized as «slow-moving», «fast-moving», or «non-moving».
Compared: LIFO and FIFO
First-in, first-out (FIFO) and last-in, first-out (LIFO) are two accounting methods (sometimes referred to as “costing”) that are dependent on the order in which goods enter and exit your warehouse.
Businesses that prioritize the sale of aged inventory items can benefit from FIFO. When a consumer places an order, the merchandise that arrived first at the distribution center should be given priority. The supply of perishable items must be preserved for as long as possible.
LIFO, unlike FIFO, prioritizes the sale of the most recently received inventory. Due to the nature of LIFO's revenue presentation, it is most suitable for businesses that do not ship perishable products. By default, the FIFO pricing method is used.
JIT inventory management
The just-in-time inventory system, also referred to as JIT inventory, is particularly suitable for companies that have minimal stock requirements. This method is commonly employed by businesses that do not rely on large inventory but instead fulfill orders as they are received. Under normal circumstances, there is a harmonious equilibrium between the number of orders placed and the quantity of stock on hand.
The JIT methodology is highly effective for businesses that operate in industries where perishable or time-sensitive goods are involved. As the market for their products expands, they have the capability to fulfill orders that perfectly align with their customers' demand. Once the season ends, the concern of financial loss on perishable goods will be eliminated, allowing them to prioritize inventory management and clearance.
Companies that profit from consumer trends cannot afford this strategy. As a result of sudden spikes in demand, particularly COVID-19, a number of industries confronted pricey stock-outs in 2020.
There are risks associated with JIT inventory management. In the event of an abrupt increase in demand, the company may be unable to acquire sufficient supplies, resulting in reputational harm and a loss of customers to rivals. Even if a critical input is not received «just in time», a bottleneck may develop despite the minimal delay.
Forecasts of Interest
Demand forecasting (also known as sales projections) may aid in ensuring that you always have enough of each product in stock to satisfy customer demand.
In order to make accurate forecasts, established businesses must examine their historical sales data. A business may have to rely on educated guesses and market data until it has established a sound sales track record.
In order to determine how much of a particular product should be kept in stock at any given time, supply chain management heavily relies on accurate demand forecasts. Based on the results of a quarterly evaluation of the demand forecast, minimum quantities and reorder points may be modified.
Establishing an Infrastructure for Scanning
You should seize the opportunity to automate a process that previously required human intervention.
Barcodes are inexpensive, whereas human error can be very expensive.
Products should be scanned whenever they are received, transferred, transported, or otherwise modified. Without a scanning solution, your business is susceptible to innumerable human errors, misspelled SKU numbers, and inaccurate inventory data.
This is a significant issue when your online store must stock more than a few items from a single location.
Drop delivery
Dropshipping is one of the most popular and accessible inventory management strategies currently available. It is not as simple as a regular inventory count because business owners do not have direct access to the products. As business proprietor, you are responsible for both receiving and delivering orders from suppliers. You never have any contact with the stock.
This is a common strategy for new online retailers without the capital to invest in a warehouse who wish to expand swiftly.
Although dropshipping may appear effortless, you have no control over the consumer service they receive. After a customer makes a purchase, manufacturers frequently manage the majority of the work, including product storage and shipment. A client may seek your assistance if they have received incorrect or defective goods.
Comparing quantity requirements and their economic equivalents
Companies might benefit from knowing the minimum order quantity (MOQ) and economic order quantity (EOQ) when planning how often to reorder products.
The minimum order quantity (MOQ) is the lowest possible order total that a certain vendor is willing to fulfill for a given product type. Minimum orders for expensive goods are typically smaller than those for inexpensive ones. When placing fresh orders with suppliers and comparing the MOQ of a specific vendor to your own sales projections, it is vital to keep this in mind.
The EOQ method is commonly used in manufacturing because to the inherent uncertainty in raw materials, production, and demand. The program enables firms to buy a wide range of products in bulk, with the goal of reducing the frequency with which individual items must be reordered.
Initial in, initial out
The “first in, first out” policy is favored by retailers when selling perishable products. Therefore, the term “first in, first out” (FIFO) refers to the order in which products are dispatched to customers.
It is not limited to establishments that sell perishable merchandise. This management strategy can be utilized by any company that needs to quickly dispose of excess stock. Keep a close watch on the prices of your goods and equipment, however. Consistent price adjustments can increase profits by widening the gap between expenditures and revenue.
Additionally, LIFO and FIFO are utilized by retailers who sell perishable goods as supplementary inventory systems.
Parallel docking
Cross-docking is a time-saving technique that emphasizes efficiency. A delivery truck will unload at your business, and then load up onto cars that will convey your sales to customers. This eliminates the need for your warehouse to be restocked and bypasses the standard stock-taking procedures. Instead, we dispatch your order once payment is received. This method is beneficial for “just in time” product delivery.
The number of days an item has been in inventory, as determined by the days sales in inventory (DSI) system.
This financial ratio displays the average time it takes for a company to convert its inventory into revenue, encompassing products that are still in the development phase. The interpretation of the performance statistic, days sold in inventory (DSI), can vary depending on the specific context. The term “days inventory” is used interchangeably with several other names, such as “days old inventory”, “average inventory age”, and “DIO”.
This metric discloses the lifespan of a company's current stock in order to gauge the liquidity of a company's inventory by measuring how long the stock has been in circulation. In spite of the fact that the typical DSI fluctuates from industry to industry, it is generally accepted that a lower DSI is preferable because it suggests a shorter amount of time required to sell off the inventory.
Additional provisions
Retailers commonly use safety stock as an additional method for managing inventory in the event of unexpectedly elevated demand. In contrast to the JIT method, which relies on anticipating and responding to supply and demand fluctuations, safety stock enables you to maintain constant production.
Inaccurate demand projections, shifting consumer preferences, and fluctuating lead times for various basic materials are a few of the reasons why retailers maintain a safety stock. You have a fighting chance of weathering these storms if you maintain a buffer of extra supplies on hand.
MRP stands for Material Requirements Planning
In order to accurately foresee inventory demands and alert material suppliers in a timely manner, this inventory management method requires producers to maintain detailed sales records. In anticipation of consumer demand, ski factories utilizing MRP inventory systems might stock up on plastic, fiberglass, wood, and aluminum. The manufacturer's inability to precisely predict sales and plan inventory purchases hinders its ability to meet customer demand.
Inventory Management Software
Inventory management software refers to software designed specifically for managing stock and orders. Assists businesses in predicting demand, coordinating the flow of products, and monitoring stock levels in real time so that they always have exactly what they need. By automating tasks such as order creation, shipment tracking, and reordering, inventory management software can help businesses increase efficiency, reduce stockout risks, and streamline supply chain processes.
Utilizing optimal practices for inventory control
Inventory is your company's most valuable asset. Consider it to be a unit. Utilizing inventory management strategies such as those described above enables you to make more informed purchasing decisions, acquire a greater understanding of your warehouse's contents, and streamline operations.
Keeping track of what enters and exits your business requires systematic procedures such as inventory counts, audits, and restocking. Utilizing the proper inventory management strategies and resources will allow you to maintain a continuous supply of the products that attract new consumers. Everyone can contribute to increasing productivity and profits at work when they labor together.
FAQs
What is inventory management exactly?
Inventory management involves monitoring and storing products to meet demand effectively. It ensures products are available when needed and helps control costs related to stocking and storage.
Why is inventory control so important?
Inventory control is crucial because it affects various aspects of a business, including profitability, customer satisfaction, and operational efficiency. Effective control can prevent stockouts, reduce storage costs, and optimize pricing.
How do online retailers maintain track of their stock levels?
Online retailers use various methods, including inventory management software, ABC analysis, demand forecasting, and automated scanning to keep track of their stock levels and ensure accuracy.
Why is systematic inventory management important?
Systematic inventory management is crucial for businesses to maintain accurate records of what enters and exits their operations. It involves procedures like inventory counts, audits, and restocking, which are essential for maintaining a steady supply of products and increasing productivity and profits.
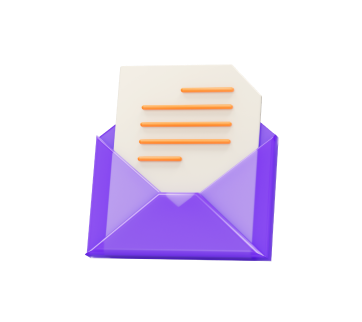