Outbound Logistics: Efficient Processes for Business Success
Content Writer
Outbound logistics refers to the intricate process of moving finished products from a company’s warehouses to its end customers. This aspect of supply chain management focuses on ensuring that goods are delivered accurately, efficiently, and in the best condition. Businesses rely on well-structured outbound logistics systems to meet customer expectations, reduce costs, and maintain competitiveness in today’s fast-paced market.
Effective outbound logistics begins with robust planning and coordination. It involves managing inventory, preparing products for shipping, and optimizing transportation methods. Each step, from order processing to delivery, is designed to streamline the flow of goods and ensure that customers receive their products on time.
A successful outbound logistics strategy enhances customer satisfaction and minimizes operational inefficiencies. For instance, leveraging technology such as real-time tracking systems and automated inventory management tools can significantly reduce errors and improve transparency across the logistics chain. By integrating these technologies, businesses can monitor shipments in real-time, address issues proactively, and provide accurate delivery updates to customers.
Moreover, outbound logistics serves as a critical touchpoint for building customer trust. Timely and reliable deliveries leave a lasting impression and strengthen customer relationships. Companies like Amazon and Walmart have set high standards in outbound logistics by prioritizing speed, accuracy, and convenience, demonstrating how efficient logistics processes can drive business success.
In addition to enhancing customer experience, efficient outbound logistics also contributes to cost savings. By consolidating shipments, optimizing delivery routes, and using data analytics, businesses can reduce transportation costs and maximize resource utilization. These practices not only boost profitability, but also align with sustainability goals by minimizing fuel consumption and reducing carbon emissions.
Ultimately, outbound logistics is more than just moving goods; it’s about creating a seamless connection between businesses and their customers. A well-executed outbound logistics system ensures that products arrive at the right place, at the right time, and in the right condition—a critical factor for achieving business success in competitive industries.
Outbound Logistics: Definition, Main Objective, Tasks
Definition of Outbound Logistics
Outbound logistics is a vital part of supply chain management, focusing on the movement of finished goods from warehouses or production facilities to end customers. It encompasses a series of processes, including inventory management, order fulfillment, transportation, and delivery, all aimed at ensuring that products reach their destination accurately and efficiently.
This process involves multiple stakeholders, such as manufacturers, logistics providers, and retailers, working in unison to deliver a seamless customer experience. Unlike inbound logistics, which deals with the supply of raw materials and components into a business, outbound logistics concentrates on the flow of finished goods out of the organization.
Main Objective of Outbound Logistics
The primary goal of outbound logistics is to ensure timely, accurate, and cost-effective delivery of goods to customers. Achieving this objective requires:
- Customer Satisfaction: Delivering the right products to the right place at the right time.
- Operational Efficiency: Streamlining processes to minimize delays and reduce costs.
- Quality Assurance: Maintaining the integrity and quality of goods throughout the logistics chain.
- Scalability: Building systems that can adapt to changing demands and market growth.
By focusing on these elements, businesses can not only meet but exceed customer expectations, fostering long-term loyalty and a competitive edge.
Tasks of Outbound Logistics
Outbound logistics comprises several interconnected tasks that ensure the smooth flow of goods from warehouses to customers. Key tasks include:
- Order Management: This involves receiving, verifying, and processing customer orders. Efficient order management systems reduce errors and ensure timely fulfillment.
- Inventory Control: Proper inventory management ensures that the right products are available for dispatch. Technologies like real-time inventory tracking help avoid stock outs or overstocking.
- Packaging and Labeling: Products are securely packaged and labeled with essential details, such as shipping addresses, barcodes, and handling instructions. This step ensures safe transit and easy tracking.
- Transportation Planning: Selecting the appropriate carriers, optimizing routes, and scheduling deliveries to minimize costs and delays. Transportation planning plays a crucial role in maintaining customer satisfaction.
- Delivery Coordination: Coordinating the final delivery of goods to customers, including tracking shipments and addressing any delivery issues promptly.
Each of these tasks contributes to the overall efficiency and success of outbound logistics. By optimizing these processes, businesses can reduce operational bottlenecks and enhance their service quality.
Advantages of Outbound Logistics
Efficient outbound logistics offers numerous advantages that drive both customer satisfaction and operational excellence. These benefits span various aspects of a business, including cost management, customer experience, and scalability. Below are the key advantages:
- Enhanced Customer Satisfaction
Timely and accurate deliveries are the cornerstone of customer satisfaction. When customers receive their orders on time and in excellent condition, it builds trust and fosters loyalty. Companies like Amazon excel in this area by leveraging advanced logistics systems that ensure swift and precise deliveries.
- Cost Efficiency
By optimizing transportation routes, consolidating shipments, and utilizing data analytics, businesses can significantly reduce logistics costs. Efficient planning minimizes fuel consumption and reduces the need for expedited shipping, contributing to overall cost savings.
- Streamlined Operations
Automated processes in outbound logistics, such as real-time tracking and inventory management, eliminate manual errors and improve workflow efficiency. This streamlining allows businesses to handle higher volumes of orders without compromising quality.
- Competitive Advantage
Companies with efficient outbound logistics systems can offer faster and more reliable deliveries, giving them a distinct edge over competitors. For example, Zara’s quick replenishment system ensures its stores are always stocked with the latest trends, enhancing its market position.
- Scalability and Flexibility
Well-structured outbound logistics systems are designed to scale with a business. As demand grows, these systems can adapt to handle larger volumes, new delivery destinations, or additional services without significant disruptions.
- Sustainability Initiatives
Optimized logistics processes contribute to sustainability by reducing fuel consumption and emissions. Consolidated shipments and efficient route planning minimize the environmental impact of transportation, aligning with modern sustainability goals.
By capitalizing on these advantages, businesses can not only improve their logistics performance but also strengthen their market presence and long-term profitability.
Steps of Outbound Logistics
1. Order Processing
Order processing is the foundational step in outbound logistics. It begins with receiving and verifying customer orders to ensure accuracy. This process involves checking inventory availability, confirming payment details, and generating necessary documentation such as invoices and shipping labels. Automated order management systems can significantly accelerate this process, reduce errors, and ensure timely fulfillment. For instance, companies like Amazon use advanced software to handle millions of orders daily, ensuring seamless operations.
2. Consolidation into Transport Units
Once orders are processed, they are grouped into larger transport units, such as pallets or containers, to optimize handling and shipping efficiency. Consolidation minimizes the number of trips required for delivery, reducing transportation costs and environmental impact. Proper planning during this step ensures that goods are securely packed, preventing damage during transit. Businesses often rely on logistics software to determine the most efficient way to consolidate shipments.
3. Pick-Up, Packaging, and Labeling
The next step involves retrieving products from inventory, securely packaging them, and labeling them with detailed shipping information. Packaging protects the products from damage, while labeling ensures proper identification and tracking throughout the logistics chain. Modern logistics systems use barcode scanners and RFID technology to streamline this process, reducing errors and enhancing traceability. For example, labeling often includes essential details like customer addresses, tracking numbers, and handling instructions.
4. Loading
In this step, goods are carefully loaded onto transport vehicles. Efficient loading practices maximize the use of available space while ensuring the safety of the products during transit. Logistics teams often employ load planning software to determine the best arrangement of goods within a vehicle. Proper loading also contributes to fuel efficiency by distributing weight evenly, which is especially important for long-haul deliveries.
5. Delivery
Delivery is the final step in the outbound logistics process. It involves transporting goods to their final destination, whether it’s a customer’s doorstep or a retail store. Optimized delivery routes and real-time tracking systems are critical in this stage to ensure timely arrivals and accurate updates for customers. Companies like Walmart and FedEx use advanced route optimization tools to minimize delays and enhance customer satisfaction. Delivery also includes addressing any last-mile challenges, such as traffic congestion or remote locations, to ensure the smooth completion of the logistics process.
By following these steps meticulously, businesses can create a reliable outbound logistics system that enhances operational efficiency and customer satisfaction.
Important KPIs of Outbound Logistics
Key Performance Indicators (KPIs) are essential metrics that help businesses evaluate the efficiency and effectiveness of their outbound logistics processes. By monitoring these KPIs, companies can identify areas for improvement and implement strategies to optimize their operations. Below are the most important KPIs in outbound logistics:
- On-Time Delivery Rate
This KPI measures the percentage of orders delivered to customers within the promised timeframe. A high on-time delivery rate reflects efficient planning, reliable transportation, and effective coordination among logistics teams. Consistently meeting delivery deadlines enhances customer satisfaction and builds trust.
- Shipping Accuracy
Shipping accuracy tracks how often the correct products are delivered to the right customers without errors. Mistakes in shipping, such as wrong items or incorrect quantities, can lead to customer dissatisfaction and additional costs for returns or replacements. High shipping accuracy indicates a well-organized logistics system and attention to detail.
- Transportation Costs
This metric evaluates the total expenses incurred during the shipping process, including fuel, labor, vehicle maintenance, and tolls. By analyzing transportation costs, businesses can identify opportunities for cost reduction, such as optimizing delivery routes or consolidating shipments to minimize trips.
- Order Fulfillment Time
Order fulfillment time measures the duration from when a customer places an order to when the product is delivered. A shorter fulfillment time indicates an efficient logistics process that prioritizes speed without compromising accuracy or quality. This KPI is particularly critical for businesses in e-commerce and fast-moving consumer goods.
- Inventory Turnover
Inventory turnover measures how quickly a company sells and replenishes its stock. High turnover rates suggest effective inventory management and strong demand for products. For outbound logistics, this KPI ensures that products are dispatched promptly, reducing storage costs and preventing obsolescence.
- Damage Rate
The damage rate tracks the percentage of goods that are damaged during transit. A low damage rate signifies proper handling, secure packaging, and careful transportation practices. Minimizing product damage is vital for maintaining customer trust and avoiding financial losses.
- Customer Satisfaction Score
This KPI assesses customer feedback on the delivery process, including timeliness, product condition, and overall experience. Positive customer satisfaction scores reflect the success of outbound logistics in meeting or exceeding customer expectations.
By focusing on these KPIs, businesses can gain valuable insights into their logistics performance, identify inefficiencies, and implement data-driven improvements. Monitoring these metrics regularly ensures that outbound logistics processes remain aligned with organizational goals and customer needs.
Challenges of Outbound Logistics
Managing outbound logistics effectively requires addressing several complex challenges that can impact the efficiency and reliability of the supply chain. Below are the most common challenges and how they affect businesses:
- Rising Transportation Costs. Transportation costs, including fuel prices, driver wages, and vehicle maintenance, continue to rise, placing a significant financial burden on businesses. Companies must find ways to optimize routes, consolidate shipments, and negotiate better rates with carriers to mitigate these costs.
- Last-Mile Delivery Issues. The final leg of delivery, known as last-mile delivery, is often the most expensive and time-consuming part of the logistics process. Challenges such as traffic congestion, remote delivery locations, and changing customer availability can lead to delays and increased costs.
- Meeting Customer Expectations. Modern consumers demand faster delivery times, real-time tracking, and flexible delivery options. Businesses must invest in advanced technologies and efficient processes to meet these high expectations while maintaining cost-effectiveness.
- Inventory Management. Maintaining the right inventory levels is critical but challenging. Overstocking can lead to increased storage costs, while understocking risks delays and missed sales opportunities. Real-time inventory tracking systems are essential for addressing this challenge.
- Regulatory Compliance. Navigating international trade regulations, customs procedures, and local delivery laws can complicate outbound logistics. Non-compliance can result in fines, delays, and reputational damage.
- Technological Integration. Implementing and maintaining advanced logistics technologies, such as real-time tracking systems and route optimization software, requires significant investment and expertise. Businesses must ensure that these technologies are integrated seamlessly into their operations.
- Environmental Concerns. Sustainability is a growing concern in logistics. Companies face pressure to reduce their carbon footprint by adopting greener transportation methods and optimizing delivery routes.
By understanding and addressing these challenges, businesses can improve the efficiency of their outbound logistics processes, enhance customer satisfaction, and maintain a competitive edge in the market.
Examples from Outbound Logistics
Zara
Zara’s outbound logistics system is a model of efficiency, built around speed and adaptability. The company’s vertically integrated supply chain allows it to control every aspect of production and distribution. Centralized warehouses serve as the backbone of its logistics network, enabling Zara to deliver products to stores in just a few days. By maintaining proximity to its European distribution centers, Zara minimizes transit times and ensures quick replenishment of stock. This approach allows the brand to stay ahead of fast-changing fashion trends and maintain high levels of customer satisfaction.
Zara also employs advanced technology to track inventory levels in real-time. This ensures that stores receive the exact quantities needed, reducing overstock and waste. Additionally, the company’s commitment to frequent, smaller shipments helps maintain freshness and align with current customer demands.
Walmart
Walmart is a global leader in logistics innovation, leveraging data-driven solutions to optimize its outbound logistics. The retailer’s massive distribution network includes over 150 distribution centers strategically located across the United States. These hubs are equipped with state-of-the-art technology to manage inventory, sort goods, and schedule deliveries efficiently.
One of Walmart’s key strengths is its use of predictive analytics to forecast demand. This allows the company to allocate resources effectively and ensure products are always available on store shelves. Walmart’s commitment to low prices is supported by its ability to minimize transportation costs through route optimization and consolidated shipments.
Additionally, Walmart partners with third-party carriers to enhance last-mile delivery services. By integrating its systems with those of its partners, Walmart provides real-time tracking updates to customers, improving transparency and trust.
Amazon
Amazon sets the gold standard for outbound logistics with its innovative and customer-centric approach. The company’s extensive network of fulfillment centers, coupled with advanced robotics and automation, enables rapid order processing and dispatch. Amazon’s use of machine learning algorithms optimizes inventory placement, ensuring that products are stored close to areas of high demand.
One of Amazon’s standout features is its last-mile delivery strategy. The company leverages a mix of delivery methods, including its proprietary Amazon Logistics service, partnerships with local carriers, and emerging technologies like drones and autonomous vehicles. These innovations enable Amazon to offer same-day or next-day delivery to millions of customers worldwide.
Real-time tracking and proactive communication are integral to Amazon’s logistics excellence. Customers receive updates at every stage of the delivery process, from order confirmation to final delivery. This transparency enhances the overall customer experience and reinforces Amazon’s reputation for reliability.
In addition to its operational efficiencies, Amazon is committed to sustainability. The company’s Climate Pledge initiative aims to achieve net-zero carbon emissions by 2040. This includes investments in electric delivery vehicles, renewable energy, and optimized packaging solutions.
FAQ
1. What are the applications of outbound logistics?
Outbound logistics has broad applications across industries, ensuring that finished products are efficiently delivered to end customers, retail outlets, or distribution centers. In the retail sector, it helps manage large-scale shipments to multiple store locations, while in e-commerce, it enables fast and reliable deliveries directly to consumers. Industries like manufacturing also rely on outbound logistics to transport goods to distributors or clients, ensuring timely fulfillment of orders and maintaining supply chain integrity.
2. What is the difference between inbound and outbound logistics?
Inbound logistics focuses on the movement of raw materials and supplies into a business from suppliers. It encompasses tasks like procurement, transportation, and storage of these materials for production. Outbound logistics, on the other hand, deals with the distribution of finished goods from the company to end customers. While inbound logistics emphasizes preparation and production readiness, outbound logistics is centered on customer satisfaction and efficient delivery processes.
3. What are the main components of outbound logistics?
The key components of outbound logistics include: order management, transportation, inventory management, packaging and labeling, and delivery.
4. How can outbound logistics be optimized?
Optimizing outbound logistics involves leveraging technology and strategic planning to improve efficiency and reduce costs. Key strategies include: using route optimization software, implementing real-time tracking, consolidating shipments, investing in automation.
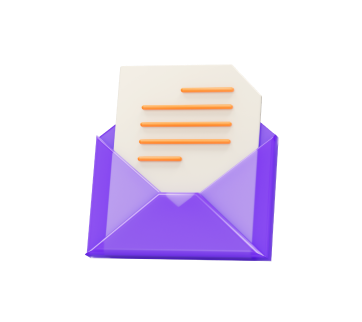