Maximize Efficiency with the Best Inventory Management Software
Content Writer
- Reasons why inventory control is crucial
- What is inventory management software, and what is it used for?
- Benefits of inventory management software
- Types of inventory management software
- How should one choose a suitable inventory control program?
- Within this section, a comparison of the most effective inventory control systems is presented
- FAQ
For the moment, you may consider your company's inventory to be its beating heart. When everything is stable and under control, business goes off easily, profits soar, and customers are satisfied. This link forms because of a correlation between the two. When stock gets out of hand, whether it's because of too much of the wrong things or not enough of the necessary ones, it will have a negative impact on your company's bottom line. Since you won't be able to manage your stock at all. Too many businesses fall flat on their faces because they can't keep their footing in this complex dance.
When seen in this light, inventory control software demonstrates its value and potential to affect substantial change, rather than merely being another tool. Further benefits include less uncertainty in stock control, process automation, insight generation, and inventory management assistance. Just pretend for a second that you have the incredible ability to predict what people will wear in the future, when they will need new products, and how to put an end finally to companies who have excess inventory and unreliable clients.
Having the ability to thrive in a data-rich environment is just as crucial as having the ability to survive in such an environment. This post will go over the basics and then some as we investigate how the ideal software may entirely change the game when it comes to inventory management. The fact is that this is true regardless of the structure of your organization, be it a small startup with few resources or a multinational conglomerate with distribution locations worldwide. We will examine several technologies that may make your inventory work harder than you do so that your firm can stay competitive, efficient, and ready for everything the future brings.
Reasons why inventory control is crucial
The capacity to maintain command of the stock is crucial.
To thrive, companies need a system that allows them to monitor and manage their inventory levels. This is particularly the case for businesses operating in the wholesale and manufacturing sectors. This allows companies to prevent stock outs, which can result in lost sales opportunities, and reduce the amount of cash sitting on unsold items, which are two crucial aims. This is the direct cause of both of these aims.
Companies may reap the benefits of having an effective inventory control system in a number of different ways, some of which are listed below:
- Maintaining an acceptable level of control over the expenses associated with transporting goods is an essential aspect to consider.
- Eliminating the possibility has the effect of lowering the probability that the outstanding may become unsatisfactory or outdated.
- By keeping the inventory at the ideal levels over the course of time, it is feasible to maximize the flow of cash without sacrificing efficiency.
- Make sure that the things are not difficult to get to increase the degree of pleasure that the clients have during their encounter.
- Make use of your experience to execute manufacturing and purchasing transactions!
It is possible for companies to increase operational efficiency and overall profitability by using effective inventory control systems. The company stands to gain from this situation. Perhaps these goals can be achieved with the help of inventory management software, which offers the necessary resources and critical information.
What is inventory management software, and what is it used for?
Many processes that take place inside a company may be automated with the help of inventory management software. Order processing and inventory management are all part of this domain. Helping businesses save money and run more efficiently is the ultimate aim of keeping track of inventory goods, customer orders, and incoming deliveries. The main goal is to help businesses improve their supervision.
Organizations in the manufacturing sector depend substantially on inventory control systems to maintain tabs on production documentation, raw materials, and components. This kind of action is required by the demands of the industrial sector. To keep the production process running smoothly, this is done whenever it is necessary. This category includes a wide variety of documents, such as work orders and invoices for the purchased products. Not only that, but those aren't even the most basic examples of what this category covers.
One of the several tasks performed by an inventory manager is maintaining a record of the tangible items housed in the business's storage facility. This is one of several activities involved in inventory management. Inventory management encompasses a wide range of activities. This is simply a small portion of the whole process of inventory control, which encompasses a great deal of other tasks as well. The key to efficient inventory management is having a firm grasp on what has to be categorized in each part. You will be able to keep an accurate count of your stock using this. Taking both of these factors into account at once allows for a precise assessment of the basic resources and the final goods derived from them.
Part of keeping track of your inventory is also making note of what your most loyal customers and business associates have on hand. As part of inventory management, this is also included. Independently tracking all of these components can be a huge challenge for small and medium-sized businesses (SMBs) that rely only on spreadsheets. A piece of software that connects your company's data systems with data about the commodities stored in inventory is what the phrase “inventory management software” represents.
You will have access to the information that is being described here if you make sure your inventory is managed appropriately. Making an informed decision about which software is best for your business may be challenging when you have to think about both the capabilities your employees need and how much the program will cost. This is because you will be compelled to consider these two factors. This is because the software's worth may exceed the features really needed for the application to run well. This is because it is not only possible, but also highly feasible, for you to think about both of these things simultaneously. The purpose of this review roundup was to lend credibility to the ongoing effort by giving relevant and useful information. We read up on seven distinct inventory management systems and compared and contrasted them all to get this objective.
The term “inventory management” may make it sound like a simple way to keep track of your possessions, but in reality, there are many different features that make up inventory management software. You can't have one without the other of these unique qualities. It is crucial that the application performs as expected so that your accounting software or enterprise resource planning (ERP) system can communicate with it. You must ensure that this condition is met before the software can effectively operate. With the help of an inventory management system, you can keep track of the worth of the things that make up your inventory for accounting purposes. It is within the realm of possibility to do this. It is feasible to achieve this, as this is the system's primary goal. In the end, you'll be able to leverage this to your advantage by creating reliable financial statements. Not only can you utilize this system to keep track of the products kept in various warehouses, but it will also give each item a value, typically in many currencies. You will be able to accomplish both of these goals with this.
The use of software offers several advantages that should be considered while managing inventories. These advantages for the company are a result of the program's utilization.
One of the primary goals of the program is to make certain that the entire warehouse area is neatly organized and can be observed without difficulty from any point outside. Because there is a lack of transparency and accountability in the processes that are used to manage the central warehouse, there is a risk that the fulfillment of follow-up responsibilities may result in probable inefficiencies as well as additional expenditures coming from the performance of these duties.
Examples of the kinds of duties that fall under this category include rework that occurs as a result of inaccurate or missing inventory data or bottlenecks in the supply chain that have an impact on the ability of your customers to acquire items. This is just one example of the kinds of obligations that fall under this category. The capacity of your clients to buy items may be impacted by the many sorts of tasks that they are responsible for.
Benefits of inventory management software
There is a broad variety of uses for inventory management software, and it can totally revolutionize the way in which organizations function through its implementation. Inventory optimization can change the management of your supply chain in a number of different ways, one of which is by implementing the following examples.
Some of the ways in which accuracy has improved include the following:
- It is now less frequent for people to make mistakes when it comes to inventory control and order fulfillment.
- Creating reports effectively and automating the process of data entry are both activities that have the potential to save time.
- Measures to reduce spending: The optimal inventory levels serve to reduce carrying costs and minimize overstocking, both of which are key variables to consider while making inventory decisions.
- Improvements in decision-making skills, including insights generated from data for the purpose of developing more intelligent purchasing and forecasting methods.
- By integrating inventory control with other company activities, we may be able to enhance the operations of the corporation and construct workflows that are more streamlined.
- It is possible to make the most efficient use of storage space thanks to the software, which enables the reliable collection of inventory data and the supply of suggestions for the most effective allocation of storage space.
- There was a reduction in the financial loss that was experienced because of running out of particular commodities or overstocking, which led to an improvement in profitability. Additionally, there was an increase in the number of sales opportunities that were generated, which led to an improvement in profitability.
- Using the real-time data and analytics that are generated by warehouse management systems on inventory, performance, and production, customers can better lead their operations and make choices. This is because they can better understand their operations. The result is that customers can make better judgments overall.
- If a small company has reliable warehouse management software that can expand along with them and meet their growing demands, then it is feasible that they will be able to increase their warehouse management without experiencing any kind of interruption whatsoever as their business grows.
- It is possible that consumers would see faster delivery times because of the use of warehouse management software that streamlines operations and offers quick access to inventory data. Processes are simplified as a result of the program's implementation. This is something that can be accomplished with the help of an order fulfillment system that is more efficient.
With the assistance of warehouse management software, which has the capability to enhance data integrity, the number of mistakes that occur while manually tracking warehouse movements may be decreased. This is because the program can improve data integrity.
Types of inventory management software
There are many different inventory management solutions that are compatible with a wide range of computer systems. It is possible to use any one of these many solutions.
When it comes to inventory management systems, there is a vast range of options available to choose from to meet the individual needs of a diverse range of enterprises. These kinds of systems may be found in a wide range of various applications, since they are versatile. The following are some instances of it, although there are a huge number of different sorts all together.
The assistance that organizations need to meet this requirement is supplied by inventory management systems that are independent of one another. This is because these systems are unique in that they can monitor stock levels, orders, sales, and delivery without affecting one another.
The application applicants that are the most qualified are those small and medium-sized businesses that are seeking inventory management systems that are streamlined down to their most essential components.
Two instances that illustrate this notion are applications like Flow Inventory and Zoho Inventory. Both of these applications are examples.
The software that is used for inventory management is a component of a larger enterprise resource planning (ERP) system. This ERP system also includes software for accounting, human resources, and customer relationship management, among other areas of software development. As an additional feature, this enterprise resource planning system incorporates software for customer relationship management. One of the components that constitute the enterprise resource planning system is this program.
Excellent candidates for this solution are larger businesses that require solutions that can be applied across several departments.
There is software like Microsoft Dynamics 365, Oracle NetSuite, and SAP ERP, to mention just a few examples of such software.
Warehouse management systems (WMS) are designed to handle a wide variety of warehouse procedures, including receiving, picking, packing, and shipping, to name just a few of the many processes that include warehouses. The supply of tailored solutions for a wide range of assignments is the core purpose of this company.
Companies that have extensive storage needs, such as big distribution centers, are ideal candidates for implementing this method because of the complexity of their storage requirements.
Examples of firms that would profit from this include Fishbowl Warehouse, Blue Yonder, and the WMS from Manhattan Associates. These are all excellent examples of enterprises.
Order management systems, often known as OMS, are gaining popularity among organizations as a method of enhancing their capacity to handle the processing of data across various channels. This includes the administration of sales orders, inventory levels, and choices regarding fulfillment.
Companies that deal in large quantities or that utilize a multitude of sales channels, such as online marketplaces, would be extremely interested in purchasing this product because of its widespread appeal.
The following platforms can include order management systems (OMS) into their operations: Orderhive, Brightpearl, and Shopify are those three.
Perpetual inventory systems are meant to continually and in real-time monitor the products that are in stock. This is accomplished through the usage of barcode scanners or RFID technology.
Those manufacturers and merchants who are looking for dependable inventory data that is updated on a minute-by-minute basis will find this solution to be of great assistance.
Lightspeed Point of Sale (POS) and Square are not excluded from this coverage when it comes to retail.
Keeping track of things that are sold in several places is made much simpler by the utilization of software designed specifically for retail inventory management. It is commonly used to interact with point-of-sale (POS) systems in retail settings, which is to be expected given its intended application.
If all goes according to plan, the candidates would be shops that have a presence across many sites or who have excellent e-commerce systems.
Vend, Retail Pro, and Clover are all products that should be considered.
Asset monitoring systems are widely utilized by firms for the purpose of keeping track of their fixed assets, which may include items such as machinery and equipment that are not immediately available for purchase. This is done to ensure that the assets are properly managed.
Businesses that have a significant number of assets that need to be inspected or maintained regularly would benefit tremendously from the use of this service because it would be of great assistance to them.
Here is a sampling of them, in no particular order: EZOfficeInventory, Asset Panda, and Snipe-IT are all examples.
Work-in-process (WIP), finished goods, and raw materials are all monitored by manufacturing inventory systems, which are sometimes referred to as MRP (Material Resource Planning) in certain circles. These systems are tasked with the job of monitoring these three categories. In addition to their other features, MRP systems frequently include production planning skills as part of their package.
This solution is perfect for businesses that need to maintain tight control over both their production and their stock at the same time.
There are many instances of these, but some of them are Odoo, Katana, and MRPeasy.
Not only that, but the application that manages stocks also incorporates demand forecasts into its functionality.
The purpose of this endeavor is to make a prediction regarding the quantity of stock that will be required by making use of predictive analytics, which considers various elements, including trends in the industry as well as historical data.
Those individuals whose requirements are prone to fluctuating often and who are looking for a solution to avoid their inventory from being either overstocked or understocked would be a great fit for this product.
Stock IQ, EazyStock, and Netstock are just a few examples of the many available options. To name just a few examples, here are several.
Businesses that are interested in enhancing their real-time stock synchronization and control across a broad number of sales channels will find that multichannel inventory management solutions are a blessing in disguise.
Businesses that offer their products on many platforms, such as their own website, eBay, Amazon, or other online marketplaces, will find this product to be an ideal solution.
A few examples of the many various applications that are available to pick from are ChannelAdvisor, Skubana, and Linnworks. There are many more.
There are a number of important aspects to consider, including the size of your company, the sector in which it works, and the inventory requirements. Each kind, from the most rudimentary inventory monitoring to the most complex warehouse management, comes with its own distinct set of benefits that make it suitable for a wide range of activities. These benefits make it possible for the system to be utilized in a number of settings.
How should one choose a suitable inventory control program?
While deciding on software for inventory control, evaluate the size, industry, challenges, and expansion goals of your business. Look for providers of scalability, real-time updates, configurable reporting, and seamless connections with current systems. Review the user interface, the availability of mobile apps, and the many client support options. Small businesses should offer solutions with affordable cost and user-friendliness top importance, as well as asset-tracking capabilities.
Real-time control and monitoring of inventories allows one to
This basic quality guarantees that, anywhere in the globe, an accurate picture of inventory is kept across all sales outlets and sites. Barcode scanning and automated data entry let companies quickly change their stock levels and create shipping labels with ease. This helps to prevent inventory from running out, reduces surplus, and allows accurate forecasting by visibility.
Real-time monitoring also ensures that departments may work closer together more successfully. Sales teams may check product availability in real time before verifying orders; the warehouse staff is informed of upcoming restocks or urgent picking needs. This openness assures that consumers will get their purchases on time, reduces the possibility of misunderstandings, and helps to lower mistakes; all of these factors assist in raising general satisfaction.
Inventory Planning and Management Optimization
Advanced inventory management systems combine past data, sales patterns, and predictive analytics to help ascertain the optimal stock levels. With consideration for lead times and seasonal variations, the system may calculate reorder points and generate suggestions for suitable order quantities. This optimization helps to lower carrying costs, minimize obsolete stock, and boost profitability by minimum prevention of such effects.
Furthermore, modern systems include dynamic safety stock estimates to include changing demand or uncertainty about the providers. They can replicate a range of events, including sales surges during marketing campaigns, thereby ensuring that companies are ready to meet consumer needs without resorting to large extra stock purchases. These preventive acts help to increase operational efficiency as well as profitability.
Forecasting demand going forward and replenishment of current inventory
Through research of past sales data and market trends, the most successful inventory control system can appropriately project future demand. Using this approach helps companies to guarantee that they provide the right products at the right times and reach optimal inventory replenishment. These ideas enable automatic reordering systems to utilize projections to keep an appropriate degree of inventory.
Furthermore, often considered by demand forecasting models are others outside variables such as changes in macroeconomic events, competitive behavior, or market conditions. Including these elements helps companies better understand the demand that will be required going forward. This ensures that businesses can manage unanticipated changes in buying patterns and keep balanced inventory levels at the same time.
Order Management and Administration and Processing
These features help to simplify and automate the whole order fulfillment process. From the manufacturing of orders to shipping and customer billing, these technologies allow exact processing at every level. They can integrate with many sales channels, including e-commerce platforms and marketplaces like Amazon and Shopify, therefore centralizing order management and presenting a consistent image of all sales activities.
Resilient order processing systems include not just integration, but also features meant to enable efficient administration of exchanges and refunds. If companies automate restocking and control return status, they can keep exact inventory levels and provide their customers with a hassle-free experience. Apart from raising operational speed and customer loyalty, this degree of competence reduces the necessary physical effort.
To optimize operations, the most effective inventory control program should be able to interface without any issues with other systems. Among the most often occurring combinations are:
- The ERP system is Inventory should line up with information from operations, accounting, and finance.
- Platforms that could have their sales, returns, and stock levels updated automatically as they happen are Shopify, Amazon, and WooCommerce.
- Order fulfillment is more effective when customer data is linked with stocks, made possible by CRM systems.
- Using shipping solutions means tracking and accelerating delivery by coordinating stocks with shipping companies.
Apart from these standard interfaces, some advanced systems also interact with marketing technologies to link inventory data with promotional activities. Companies might, for example, dynamically change the availability of products shown online depending on real-time stock changes. This guarantees that, in sales events involving many clients, correct information is given. This interconnectedness helps every department to become more efficient.
Reporting tools and analytics
Customized dashboards and reports allow one to get an understanding of inventory performance, sales trends, and profitability as well. These instruments help to calculate turnover rates, indicate opportunities for development, and identify which items are moving fast and which are slow. Real-time data and visualizations provide companies the capacity to quickly spot trends and maximize inventory planning.
Advanced analytics often incorporate predictive skills, which helps companies to project future opportunities or challenges. For example, heat maps of warehouse activity might point out inefficiencies in storage or picking processes; meanwhile, profitability studies help rank products with very high margins first. These revelations provide companies the chance to make decisions based on facts that are informed and motivated, therefore enhancing their whole performance and profitability.
Within this section, a comparison of the most effective inventory control systems is presented
1. A brief analysis of the SevDesk app
Although SevDesk primarily provides tools for accounting and invoicing, it also includes some basic skills for inventory control. Furthermore, it is particularly popular in Germany and Austria since it is designed to meet the requirements of small and medium-sized businesses (SMEs), which are the target demographic. Because it is hosted in the cloud, its architecture makes it accessible from any location. This provides owners of small businesses with the freedom to manage their inventory control as well as their money.
Character traits:
- In the process of merging accounting: The provision of streamlined accounting solutions, such as VAT computations, spending control, and automatic invoicing, is among the many items that are offered. Consequently, this ensures that your financial data and inventory are synchronized with one another.
- Controlling product listings and keeping track of stock levels are two of the fundamental aspects of inventory control.
- Interacts with e-commerce systems such as Shopify and WooCommerce to provide real-time inventory adjustments and online sales adjustments. This feature provides support for online purchasing.
- Provides users with the ability to monitor their stock levels and handle their money while they are using the product.
- The interface is intended to be simple to use and was developed with users who are not technically savvy in mind.
- Because its membership fees are affordable, it is an excellent choice for businesses that are either small or medium.
- Comprehensive backing for adherence to financial regulations, particularly in the market that is dominated by countries that speak German.
On the other hand, there are not a lot of advanced inventory control systems, such as demand forecasting or warehouse optimization.
Because its skills primarily center on financial management, it is not ideal for businesses that have inventory requirements that are significantly more complicated.
Small enterprises or sole proprietorship who are looking for a lightweight solution that combines accounting capabilities with straightforward inventory control are ideal candidates for this product.
2. A Breakdown of OpenZ briefly
OpenZ provides various open-source enterprise resource planning (ERP) applications, some of which include production oversight, financial management, and inventory management. It is a powerful alternative for medium-sized to large businesses that are looking for a solution that is suitable for their requirements without having to pay significant license charges because of its adaptability and flexibility in terms of customization.
Modular corporate resource planning systems that include modules for inventory management, financial management, procurement management, and sales management are among the most important characteristics. Users can add or delete features according to their own individual requirements.
Management of the inventory in real time includes the following:
- All the inventory levels, batch counts, and locations are monitored across a number of different warehouses.
- Integration—that is, compatibility with other systems, such as shipping providers and software developed by other developers—could be a factor in the achievement of greater process automation.
- It is possible for businesses to modify the user interface to correspond with their operations to provide a user experience that is personalized to their specific requirements.
- One of the advantages of adopting open-source software is the ability to customize it in a straightforward and cost-effective manner.
- Powerful community support that is consistently updated with new content.
- Within the scope of this document, a detailed summary of the facts concerning operations and inventories is presented.
- The ability to implement and maintain the system can only be accomplished by someone who is knowledgeable in technology.
- Only a limited number of vendors are supported, with the majority of information coming from community forums and other sources.
Companies of a medium to large size that have internal information technology teams who are capable of customizing and managing software would find this solution to be ideal.
3. An Assessment of the LogControl System
There is a company called LogControl that specializes in the administration of warehouses and the optimizing of inventories. This product is aimed at businesses that require complicated solutions to minimize inventory expenses, enhance stock accuracy, and maximize warehouse operations. The target market for this product is businesses. LogControl offers scalable solutions and services that are suitable for a wide range of sectors, including retail, manufacturing, and logistics, among others.
Aspects of the LogControl's personality:
- Advanced demand forecasting, reorder point computation, and safety stock management are some of the features that inventory optimization provides for its users.
- Inbound and outbound logistics, storage optimization, and pick-and-pack procedures are all among the functions that are supported by this comprehensive warehouse management system.
- Oracle, SAP, and Microsoft Dynamics are examples of enterprise resource planning (ERP) systems that may be easily integrated with the use of data integration.
- Using analytics tools, one can obtain information on the turnover of inventory, the use of storage space, and the performance of suppliers.
Advantages:
- Optimized for use by businesses that place a high focus on reducing costs and increasing efficiency.
- Particularly scalable, enabling both the inclusion of warehouses and the growth of business operations.
- Decisions are influenced by the comprehensive analytics at hand.
Cons:
- The price is higher than that of alternatives that are less complicated.
- Due to the sophisticated nature of its features, it is necessary for workers to undergo extensive training because of their intricacy.
Organizations that want to increase the production of their warehouses while simultaneously reducing expenses via the use of advanced inventory management systems are ideal candidates for investment.
4. A Review of Lager3000
Lager3000 is a company that specializes in the creation of warehouse management solutions for small and medium-sized businesses. It places an emphasis on simplicity and provides a basic approach to the management of operations in manufacturing facilities, including order processing and stock level control responsibilities.
- The primary characteristics include the fact that order management is responsible for handling the operations of selecting, packaging, and shipping, which simplifies the process of order fulfillment.
- Having this knowledge is made feasible by tracking inventory, which provides real-time visibility into stock levels and locations, respectively.
- In terms of design, it is convenient. The personnel's learning curve can be lowered by using user interfaces that are simple to understand.
- The resources for reporting feature provides simple reports that are intended for monitoring the performance of inventories.
- Because it is inexpensive and easy to use, it would be of tremendous benefit to less substantial organizations.
- Application-based quick implementation approach with the lowest possible technology needs based on the application process.
- That is adaptable enough to meet the particular requirements of an organization.
- For larger businesses, the system's scalability is restricted to a certain extent.
- There are two complex aspects that are absent from this product, and they are demand forecasting and automation.
It is here that the ideal fit may be found for small firms or startups who are looking for a warehouse management system that is both straightforward and competitively priced.
5. An assessment of the E+P LFS (Epg LFS)
E+P LFS is a contemporary warehouse management system (WMS) that was developed specifically for larger-scale and more complicated logistics operations. This is now something that may be found at Ehrhardt Partner Group (EPG). Considering that it can manage scenarios involving many warehouses and various customers, it is a pretty powerful choice for companies that have supply chains that are especially sophisticated.
The incoming logistics, storage, order picking, and departing activities are some of the distinguished features that are highlighted by the end-to-end warehouse management system.
- Companies can build procedures that are tailored to their own requirements when they can do so.
- Interfaces with systems for transport management and enterprise resource planning (ERP) that are standard are included in the integrated capabilities.
- By functioning in perfect harmony with automated storage and retrieval systems (AS/RS), this function enables automation to function at its full potential.
- With the ability to span a wide range of industries, it is extremely versatile and scalable.
- Aids to implementing contemporary technology for automation.
- It is capable of managing many transactions and data.
- Installation of anything requires both time and money to complete.
- Necessitates a substantial investment in both the physical infrastructure and the educational amenities.
- It is ideal for large corporations that have a sophisticated logistics infrastructure and numerous warehouses to use this solution.
6. An Overview of bizSoft
The corporate administration software known as BizSoft was developed in Austria and is an all-encompassing and comprehensive program. Inventory control, accounting, and customer relationship management are all functions that are incorporated into this application, making it an extremely flexible instrument for small and medium-sized businesses.
The process of integrating inventory control, sales management, and accounting functionality into a single module is what is meant by the term “integrated modules”.
When managing inventory, it is necessary to keep track of stock levels, orders, and data pertaining to suppliers.
It is possible to have a faultless sales experience by utilizing customer relationship management (CRM) systems, which govern client data and communication.
A number of particular features have been developed specifically for Austrian businesses, and they provide assistance with local tax and compliance.
- An adaptable tool that can handle several areas of a corporation is a positive attribute.
- In addition to the reasonable prices, the local support is of extraordinary quality.
- Making sure that Austrian rules are followed is a simple chore.
- A disadvantage is that there is less potential for growth for businesses that are larger or operate on a global scale.
- It's possible that superior inventory management solutions that include forecasting and automation won't be made available.
- Companies in Austria that are small and medium-sized and are searching for a comprehensive solution for company management will find this to be ideal.
7. An Overview of the Simple WMS System (WMS)
Easy WMS by Mecalux is a powerful warehouse management system that was developed for companies that are looking to improve their warehouse operations and logistics. Because it can be adjusted to a larger or smaller size, it is suitable for use in both small and big warehouses.
Character traits:
- The movement of commodities throughout a number of different facilities is monitored in real-time via real-time inventory management, which is monitored by management.
- By way of illustration, conveyors, and robots are examples of automated storage systems that are suitable for components of automation integration.
- The capacity to effectively manage fully automated, semi-automated, and manual warehouse layouts is what we mean when we talk about the ability to scale.
- A comprehensive knowledge of the efficacy of operations and the performance of inventories may be obtained via the use of the Advanced Reporting tool.
- The various deployment choices, which include both on-site and cloud platforms, are among the positively affecting features.
- Modified to accommodate the requirements of an individual warehouse that is either small or huge.
- There is an incredible amount of automatic assistance, and the process of setting up and operating the system is quite complicated.
- When compared to more fundamental systems, the initial investment is more expensive.
Companies of medium to large scale that are looking to maximize their warehouse operations with scalable solutions are the ideal candidates for warehouse management systems.
FAQ
What Are the Disadvantages of Warehouse Management Software?
While warehouse management software (WMS) offers significant benefits, it also comes with potential drawbacks:
- Cost: High upfront expenses for licensing, implementation, and hardware can be prohibitive, especially for small businesses.
- Complexity: Implementation and integration with existing systems require time and expertise, potentially causing temporary disruptions.
- Training Requirements: Staff may need extensive training to use the software effectively, leading to initial productivity loss.
- Dependence on Technology: Technical issues, such as system failures or connectivity problems, can disrupt operations.
- Customization Challenges: Adapting the software to unique business needs can be costly and time-intensive.
- Scalability: Some WMS solutions struggle to adapt to rapidly growing or fluctuating businesses.
In Summary: While a WMS can streamline operations, businesses should prepare for potential costs, technical dependencies, and learning curves during implementation.
What Are the Most Important Criteria in Selecting Inventory Management Software for Small Businesses?
For small businesses, selecting inventory management software involves prioritizing key factors to balance functionality and budget:
- Cost-Effectiveness: Affordable solutions, including subscription models, reduce financial strain.
- Ease of Use: User-friendly interfaces minimize the need for extensive training.
- Scalability: The software should grow with the business, accommodating increasing inventory or sales channels.
- Real-Time Tracking: Accurate, up-to-date inventory visibility helps avoid stockouts or excess stock.
- Automation: Features like auto-reordering and stock level updates save time and reduce errors.
- Integration: Compatibility with existing tools like e-commerce platforms or accounting software ensures seamless operations.
- Reporting: Basic analytics provide actionable insights for improving inventory management.
In Summary: Small businesses need affordable, easy-to-use software that supports automation, integration, and growth without overwhelming resources.
What Are the Most Important Criteria When Selecting Inventory Management Software for Large Businesses?
Large businesses face complex inventory challenges, requiring software with advanced features and robust capabilities. Key criteria include:
- Scalability: Support for multi-warehouse operations, high transaction volumes, and global expansion.
- Integration: Seamless compatibility with ERP, supply chain, and CRM systems for streamlined workflows.
- Automation and AI: Advanced tools for demand forecasting, reordering, and optimizing inventory levels.
- Real-Time Visibility: Accurate, centralized inventory data across locations and channels.
- Customizability: Tailored workflows and reporting meeting diverse departmental needs.
- Analytics: Comprehensive insights into performance, supplier efficiency, and stock trends for informed decisions.
- Compliance and Security: Adherence to industry regulations and robust data protection measures.
- Support: Reliable vendor support and training resources to ensure successful implementation and usage.
In Summary: Large businesses require scalable, highly integrated software with advanced automation and analytics to manage their complex operations effectively.
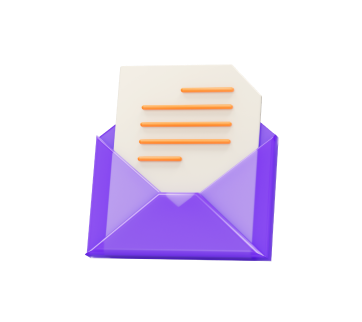